مقاوم سازی لوله بتنی با FRP
یکی از راهکارهای نوین تقویت و بهسازی خطوط لوله بتنی استفاده از پوشش های ساخته شده با کامپوزیت های پلیمری تقویت شده با الیاف FRP می باشد. خوردگی را میتوان یکی از مشکل آفرین ترین و چالش برانگیز ترین عوامل خرابی لوله های بتنی آب و فاضلاب دانست. محصولات تولید شده از فیبرهای مسلح شده با الیاف (FRP)، که دارای ویژگی هایی همچون مقاومت مناسب در برابر خوردگی، سادگی اجرا در محل نصب و سبکی می باشند، نقش کلیدی در کاهش آسیب های وارد به خطوط لوله بتنی به عنوان یکی از شریان های حیاتی خواهد داشت.
اصولا لوله های بتن مسلح را جهت انتقال آب از خارج شهر به داخل شهر به کار می برند که به شاه لوله موسومند. فشاری که این لوله ها به هنگام کار تحمل می نمایند 6 الی 35 اتمسفر است. امکان ساخت برای فشارهای مختلف، تولید در داخل کشور، مقاومت در مقابل بارهای وارده داخلی و خارجی از جمله مزایا و سنگینی و شکنندگی آنها در حمل و نقل و عدم سهولت نصب از معایب آنها محسوب می شود. با توجه به اهمیت این سازه ها به عنوان شریانهای حیاتی خدمت رسانی، خسارت و آسیب وارد بر آنها دارای هزینه فراوانی خواهد بود.
استفاده از کامپوزیت های با زمینه پلیمری (FRP) در بهسازی انواع سازه ها طی سالیان اخیر از رشد قابل توجهی برخوردار بوده است که دلیل اصلی آن نیاز به افزایش عمر بهره برداری و ارتقای اساسی زیرساختها در تمامی نقاط دنیا می باشد. سیستم های FRP بدین صورت تعریف می شود که الیاف و رزین ها برای ساخت چند لایه مرکب مورد استفاده قرار می گیرند، به نحوی که رزین های مصرفی به منظور چسباندن چندلایه مرکب به سطح مورد نظر و پوشش ها به منظور محافظت مصالح ترکیب شده استفاده می شوند. این مصالح به شکل های مختلف و درگستره ای از انواع ورقه های چند لایه کارخانه ای گرفته تا ورقه های خشک قابل پیچش روی اشکال مختلف سازه ای قبل از اضافه کردن رزین قابل دسترس می باشند.
در گذشته ای نه چندان دور مدارک فنی بسیار محدودی در این زمینه وجود داشت، لیکن امروزه تعداد قابل توجهی از مقالات علمی نشریات و کنفرانس های مربوط به بحث کاربرد FRP در مقاوم سازی اختصاص دارد. این رشد فزاینده شاهد رویکرد و اهمیت این فناوری نو می باشد که به دنبال گسترش نیاز و توجه به تقویت با استفاده از مصالح کامپوزیت و به منظور کاربردی نمودن دانش فنی، روش های طراحی نیز تدوین گردیده اند. تبیین روش های تحلیل و در نظر گرفتن ضرایب ایمنی در طراحی با ملاحظات اقتصادی منجر به تدوین دستورالعملها و آیین نامه های محاسباتی و اجرایی در این حوزه شده است.
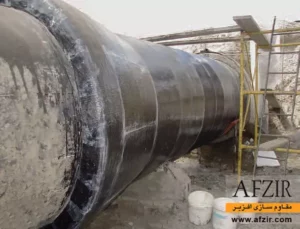
آسیب های وارد بر لوله های بتنی
به طور معمول لوله های بتنی در مقابل مواد طبیعی موجود در فاضلاب خانگی مقاوم هستند. در مواردی مثل به کارگیری لوله های بتنی به عنوان مجرای آب رودخانه، ممکن است لوله ی بتنی در برابر بعضی مواد موجود در آب رودخانه از خود حساسیت نشان دهد. در حالتی که لوله بتنی در مجاورت آب یا خاک حاوی سولفات ها، اسیدها و یا سولفید هیدروژن واقع می شود، ممکن است بر اثر حملات شیمیایی دچار آسیب شود. سولفید هیدروژن، اغلب در فاضلاب های کثیف و آلوده (مثل وجود گاز های آلوده) که دارای مسیر طولانی هستند تولید می شود. در این حالت، باکتری های بی هوازی باعث شکسته شدن مواد آلی شده و سولفید هیدروژن آزاد می کنند. سولفید هیدروژن آزاد شده در قسمت بالایی سطح مقطع لوله جمع شده و از این ناحیه، لوله را مورد حمله شیمیایی قرار می دهد. سرانجام، در این ناحیه، این مواد جمع شده به کمک باکتری های باهوازی به اسید سولفوریک تبدیل می گردد. بر اثر حملات شیمیایی، چسبندگی سیمان آسیب دیده و شسته می شود. غلظت ماده آسیب رسان به مدت زمان نگهداری و درجه ی حرارت بستگی دارد. به هر حال، آنجا که دما بالاست و یا طول مسیر فاضلاب طولانی است، امکان بروز این مشکلات زیاد است.
در لوله های انتقال آب و فاضلاب ساخته شده از بتن، آهن یا فولاد، اسید سولفوریک می تواند لوله های فاضلاب را در نقاط مختلف بویژه در تاج لوله دچار خوردگی کند و یا تخریب کند. این نوع آسیب و خوردگی لوله های بتنی آب و فاضلاب در اثر گرما و نیز در مواردی که شیب خط انتقال کم باشد تشدید شده و اثر تخریبی آن افزایش می یابد.
خوردگی را میتوان یکی از مشکل آفرین ترین و چالش برانگیز ترین عوامل خرابی لوله های بتنی آب و فاضلاب دانست. برخی از عوامل خوردگی عبارتند از:
- کلرها: اگر یون های منفی (آنیون ها) در سطح فولاد حضور داشته باشند، حتی در بتن سالم نیز امکان از بین رفتن المان تقویت کننده و یا کاهش مقاومت آن وجود خواهد داشت. تنها آنیونی که چنین اثر مخربی بر لوله های بتنی آب و فاضلاب دارد، یون کلر است. مقاوم سازی افزیر راهکارهای مناسبی برای مقاوم سازی لوله های بتنی آب و فاضلاب در برابر خوردگی کلر ارائه می دهد.
- خاکهای سولفاته: خاکی را که حاوی غلظت بالایی از سولفات های کلسیم، سدیم و منیزیم باشد را خاک سولفاته میگویند. این عامل هنگامی مخرب است که قسمتی از لوله در خاک مدفون و قسمتی دیگر در معرض هوای آزاد بوده باشد. سولفات همواره یکی از اصلی تریت عوامل آسیب و خوردگی لوله های بتنی آب و فاضلاب بوده است.
- خاکهای اسیدی: این نوع خوردگی لوله های بتنی آب و فاضلاب خیلی رخ نمیدهد مگر در خاکهای غیرطبیعی همچون خاکهایی که محتوی آلاینده هایی همچون سرباره ها و ضایعات صنعتی و معدنی باشند.
- خوردگی لوله های بتنی آب و فاضلاب در اثر دی اکسید کربن (کربناسیون): دی اکسید کربن یا رطوبت میتواند با ملات یا بتن واکنش داده و تولید کربنات کلسیم کند. این نوع خوردگی لوله های بتنی آب و فاضلاب معمولا محدود به تشکیل یک لایه سطحی می شود که خطرساز نیست؛ ولی در برخی شرایط خاص که امکان نفوذ کربنات کلسیم ایجاد میشود، خطر خوردگی فولاد تقویت کننده به وجود می آید.
عمدهترین و مهمترین نوع حمله بیولوژیكی به بتن حمله باكتریهای گوگرد در فاضلاب ها است. معمولاً در فاضلابهای خانگی این باكتریها اثر بدی بر روی بتن ندارند. در شرایط خاص مثلاً زمانی كه غلظت فاضلاب زیاد، سرعت جریان كم و درجه حرارت بالا باشد، در اكسیداسیون تركیبات معدنی و آلی گوگرد توسط باكتریهای هوازی تبدیل به اسیدسولفوریك می شود كه سطح بتن را بخصوص در حدفاصل خط آب و دیواره شدیدا میخورد. در فاضلابهایی كه تصور میشود، مقدار نمكهای سولفات بالا باشد (حدود 150 قسمت در میلیون)، باید تمام پیش بینیهای ضروری برای جلوگیری ازحمله سولفاتها به عمل آید. در چنین مواردی بهتر است برای ساختن لولههای بتنی دارای سیمان تیپ سه، آلومینات كلسیم كمتر (حدود 8 درصد) استفاده نمود. ضمنا برای به حداقل رساندن میزان نفوذ مایعات، لوله بتنی فاضلاب باید دارای نفوذپذیری پایین باشد، یعنی بتن لولهها باید دارای سیمان زیاد، نسبت آب به سیمان كم، متراكم و یكنواخت باشد.
هنگامی كه كرنشهای كششی در بتن از ظرفیت كرنش كششی آن تجاوز میكند تركها بروز میكنند. مكانیزمهای متعددی كه باعث بروز كرنشها میشوند:
- ترک های ناشی از تغییر شکل ها: این عوامل فقط هنگامی باعث كرنشهای كششی میشوند كه بتن محدود شده باشد. این محدودیت میتواند محلی باشد یا در یك محدوده بزرگ هنگامی كه جمع شدگی در یك عضو به دلیل اتصال به عضو دیگر محدود شده است. هنگامی كه یك سازه یا یك عضو سازه در مقابل تغییر شكلهای اضافی مقاومت میكند تنشها رخ داده و در نتیجه باعث بروز ترك میشوند و هر چه سازه بیشتر مقید باشد تركها بزرگتر خواهند بود.
- ترک های ناشی از جمع شدگی پلاستیک و نشست پلاستیک: ترک های جمع شدگی پلاستیك اغلب در دال ها اتفاق میافتد و تركهای نشست پلاستیك یا اسلامپ كه در عضوهای عمیق ممكن است اتفاق بیفتد و هر دوی اینها با آب انداختن بتن همراه خواهد بود. جمع شدگی پلاستیك یكی از مشخصههای بتن تازه است كه بوسیله تنشهای مویینگی در آب حفرهای بوجود میآید.
یک حالت مخصوص از تركها مربوط به تركهای نشست افقی است و هنگامی كه فواصل آرماتورها كم است ممكن است اتفاق بیفتد. این تركها باعث لایه لایه شدن در روی بالای فولادها میشوند. در موقیتهای نامناسب پوشش كف نیز ممكن است لایه لایه شود كه این امر باعث كنده شدن پوشش میشود. مكانیزم خرابی در این حالت دارای ماهیت انبساطی شبیه یخ زدن در بتن و زنگ زدگی فولاد است كه میتواند باعث كنده شدن ناگهانی پوشش در قسمتهای مهم سازه شود و در نتیجه استفاده از سازه را در معرض خطر قرار دهد.
- ترک های ناشی از بارگذاری: این تركها شامل تركهای بوجود آمده در اثر خمش، برش، كشش و … است. در هر مقطعی كه آرماتورهای پیوندی در جهت عمود بر تنشهای كششی قرار دارند تركها تحت بار سرویس عمدتا (كمتر از 0/5 میلی متر) خواهد بود. این مطلب حتی وقتی هیچ عملی جهت كنترل تركها صورت نمیگیرد به شرطی كه آرماتورها تحت بار سرویس جاری نشوند نیز صحت دارند. بیشترین نقاطی كه ممكن است تعدادی ترك وجود داشته باشد نقاط حداكثر تنش است.
- ترک های ناشی از انبساط مصالح داخل بتن: به عنوان نمونه میتوان از خوردگی فولاد در بتن نام برد.
- ترک های ناشی از شرایط موجود خارجی: اعمال بار یا تغییر شكل ایجاد شده بوسیله نشستهای متفاوت در پی بتن نمونههایی از این حالت هستند. فرمولهای متعددی برای پیش بینی تركها در بتن تحت تاثیر عوامل بوجود آورنده آنها پیشنهاد شده است ولی در آیین نامه بتن كاملترین آنها ارایه شده است. در آیین نامه تمام فرمولها، تركهایی را در نظر میگیرند كه تحت خمش، كشش، (خمش و بارمحوری) بوجود میآیند. پیش بینی عرض تركهای بوجود آمده توسط برش، پیچش و سایر اشكال بارها بطور كامل مورد مطالعه قرار نگرفتهاند، توافق بر این است كه تركهایی كه توسط بار یا تغییر شكلهای وارده رخ میدهند در موارد معمولی باعث بروز ضررهای جدی نمیشوند مشروط بر اینكه سازه از جهات دیگر اطمینان بخش باشد.
به طور خلاصه در مورد انواع آسیب و خوردگی لوله های بتنی آب و فاضلاب می توان به موارد زیر اشاره کرد:
- آسیب دیدگی بیولوژیکی و خوردگی بتن ( سولفات، کاویتاسیون، اسید و …)
- آسیب دیدگی و ایجاد شدن ترک در بتن مسلح
- خوردگی المان مسلح کننده
- لب پریدگی
- شکستگی
- سایش
- تخریب ناشی از سیکل انجماد و ذوب
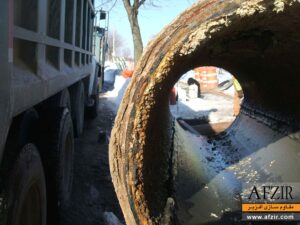
انواع روش های مقاوم سازی خطوط لوله بتنی با استفاده از FRP
سامانه های خطوط لوله به علت گستردگی و عبور از نواحی مختلف و همچنین به علت پر مولفه بودن و پیچیدگی های آن ها، در برابر خطراتی همچون زمین لرزه از آسیب پذیری بالایی برخوردار بوده و به عنوان یکی از شریان های حیاتی در کاهش و یا افزایش خسارات و آسیب پذیری ناشی از خطرات زمین لرزه نقش کلیدی دارند. خطوط لوله از جنس بتن نیز از این قاعده مستثنی نمی باشند. از اینرو انتخاب روش درست، دقیق و متناسب تعمیر و مقاوم سازی لوله بتنی آب و فاضلاب اهمیت ویژه ای برخوردار می باشد.
مهمترین روش های مقاوم سازی لوله بتنی آب و فاضلاب عبارتند از:
- تزریق اورتان در ترک ها
- تزریق اپوکسی
- تعمیرات انبساطی اتصالات
- تقویت با پوشش اپوکسی
- پوششهای پلیمری تقویت شده با فیبر
در ادامه راهکارهای نوین ارائه شده مبتنی بر استفاده از پوشش های پلیمری تقویت شده (FRP) جهت مقاوم سازی خطوط لوله بتنی، بصورت تقویت از درون و تقویت از بیرون لوله، مورد استفاده در مقاوم سازی افزیر و مکانیزم عملکرد آن ها شرح داده خواهد شد.
روش چسباندن تر در تقویت لوله های بتنی با بوشش های کامپوزیتی (Wet Lay-up Method)
در این روش الیاف خشک یک یا چند جهته در محل با رزین ها آغشته می شوند. رزین های آغشته سازی مطابق با توصیه های سازنده سیستم، همراه با آستر و بتونه های سازگار به منظور چسباندن روکش های FRP به سطوح بتن بکار می روند.
در این سیستم الیاف می توانند در یک فرآیند جداگانه به کمک دستگاه آغشته ساز با مواد رزین بارور و اشباع شده و بعد از آن روی سطح بتن نصب شوند.
فیبرهای مقاوم سازی باید مطابق با توصیه های سازنده بعد از آغشته نمودن به رزین به آرامی فشرده شده تا رزین اضافه خارج شود. قبل از گیرش رزین، حباب های هوا و طبله های موجود بین لایه ها باید خارج شوند . در آغشته نمودن فیبرها به رزین باید دقت شود که تمامی فیبرها کاملا اشباع شده باشند.
همچنین قبل از کامل شدن گیرش رزین آغشته شده مربوط به لایه قبلی، باید ورقه بعدی را بطور کامل روی سطح چسباند. در صورتی که لایه قبلی گرفته باشد، قبل از چسباندن لایه بعدی مطابق با توصیه های سازنده و مشخصات فنی پروژه باید آن را با استفاده از پاشش ماسه نرم یا مواد حلال دوباره آماده سازی نمود.
همانطور که گفته شد سیستم های چسباندن تر در محل آغشته و عمل آوری می شوند، که از این جهت مشابه بتن ریزی درجا می باشند. سه گونه متداول سیستم های چسباندن تر عبارتند از:
- صفحات تک جهته فیبر که در آن فیبرها نقش اصلی را در یک جهت ایفا می کنند.
- صفحات یا منسوجات با فیبرهای چند جهته که در آن راستای فیبرها حداقل در دو جهت می باشند.
- رشته های فیبرهای بافته شده که بدور سطوح بتن پیچیده می شوند. رشته های فیبرها در حین عملیات پیچش در محل با رزین آغشته می شوند.
از مزایای این سیستم می توان به امکان پوشش هندسه های مختلف از جمله مقاطع T شکل، آرنج شکل، زانویی و دریچه ها و موثر بودن در بازگشت مقاومت به اجزای لوله با آسیب دیدگی و خوردگی دیواره اشاره کرد. در مقابل، استفاده از کامپوزیت های ساخته شده به روش چسباندن تر به کاربردهای با میزان فشار متوسط تا پایین محدود بوده و ماهیت دستی فرآیند ساخت، آن ها را مستعد داشتن نقص و اختلاف در هندسه و خصوصیات مواد کرده است.
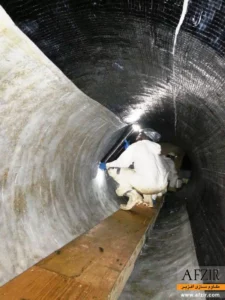
استفاده از روش بدون نیاز به حفاری در تقویت لوله های بتنی با بوشش های کامپوزیتی (RTM Technology)
در این بخش، یکی از تکنیک های تعمیر-مقاوم سازی خطوط لوله ی زیرزمینی مبتنی بر عدم حفر ترانشه ی متداول، با استفاده از پلیمر های کامپوزیتی محصولات فیبر شیشه (GFRP) و با بکارگیری تکنولوژی RTM ( Resin Transfer Modeling) شرح داده خواهد شد.
در این روش پس از تمیزکردن و آماده سازی سطح داخلی لوله آسیب دیده، یک تیوب نرم و انعطاف پذیر که از جنس الیاف تقویت کننده است، درون لوله آسیب دیده قرار داده میشود. با تزریق رزین با استفاده از تجهیزات ویژه دستگاه RTM هوای فشرده در حد فاصل بین لوله آسیب دیده و تیوب موردنظر و طی زمان لازم برای پخته و سفت شدن رزین، لوله تقویت کنندهای درون لوله آسیبدیده ایجاد میشود که نقش اساسی را در عملکرد لوله ایفا میکند. گسترش فرآیند تعمیر و مقاوم سازی خطوط لوله ی زیر زمینی از کار افتاده بر طبق فرآیند RTM نشان داده شده در شکل زیر که نیازمند زمان عملیاتی و هزینه کمتر با استفاده از تجهیزات کوچکتر و ساده تر است، شامل چهار مرحله به شرح زیر می باشد:
تکنولوژی های مبتنی بر حفاری که عموما برای تعمیر و جایگزین کردن لوله های زیرزمینی تخریب شده مورد استفاده قرار می گرفته است با مشکلاتی همچون هزینه های بسیار زیاد حفاری و خاک برداری و قرارداشتن بعضی از قسمتهای لوله در مناطقی که دسترسی به آنها به سادگی امکانپذیر نیست و همچنین در برخی موارد ایجاد ترافیک انبوه مواجه بودند. برای برطرف کردن مشکلات ناشی از تکنولوژی حفاری، تکنولوژی های تعمیر-مقاوم سازی مختلفی مبتنی بر عدم حفر ترانشه گسترش و مورد آزمایش قرار گرفته است.
مرحله اول:
همانطور که در مرحله ی a نشان داده شده است، سطح داخلی لوله ی زیرزمینی مورد نظر تمیز شده و زائده ها و برآمدگی ها از بین می رود. سپس دستگاه خودکار متحرک طنابی را از یک سمت آدم رو به سمت دیگر آن منتقل می کند. المان تعمیر کننده و مقاوم ساز که از پریفورم فیبر شیشه ای (GFRP) و دو لایه پوشش پلاستیکی تشکیل شده است، مطابق قسمت b، به یک طرف طناب متصل شده و به وسیله دستگاه سیم پیج کشیده می شود. شکل و نوع ساخت متد المان مقاوم ساز کامپوزیتی در شکل پایین نشان داده شده است.
مرحله دوم:
هر دو انتهای مقاوم سازی انجام شده در خط لوله مورد نظر با استفاده از دو درپوش نشان داده در قسمت c شکل فرآیند RTM، که از یک حلقه ای فلزی و دیسک اکریلک مطابق شکل پایین ساخته شده است بسته می شود. در ادامه هوای فشرده با استفاده از دریچه ی هوا و از قسمت دریچه ی پوشش جهت منبسط کردن سطح داخلی مقاوم سازی تامین می گردد که این عمل منجر به اتصال کامل لایه ی خارجی و فیبر شیشه (GFRP) به سطح داخلی لوله نیاز به تعمیر و مقاوم سازی شده و هرگونه چین خوردگی و اعوجاج را که در المان مقاوم ساز هنگام عملیات جایگذاری ممکن است به وجود آمده باشد را برطرف می کند.
مرحله سوم:
بعد از خارج کردن فشار در دالان به منظور کمک به جریان یافتن آسان رزین، رزین پلی استر غیر اشباع قابل سفت شدن در مقابل حرارت در پریفورم فیبر شیشه (GFRP) با استفاده از ماشین RTM و از دریجه ی رزین از قسمت دریچه ی پوشش همانطور که در قسمت d شکل فرآیند RTM نشان داده شده است تزریق می گردد. از آنجایی که پلی استر غیر اشباع از مونومرهای با ویسکوزیته ی پایین ساخته شده است، می توان به راحتی و با فشار پایین رزین را در داخل پریفورم تغذیه کرد.
مرحله چهارم:
بعد از تزریق یک مقدار از پیش مشخص شده ی رزین، ماشین RTM از دریچه ی ورودی رزین جدا می شود. سپس هوای فشرده به داخل دالان جهت مرطوب کردن یکنواخت پریفورم فیبر شیشه (GFRP) علاوه بر اتصال مناسب المان مقاوم سازی به سطح داخلی لوله مطابق آنچه در در قسمت e شکل فرآیند RTM نشان داده شده است وارد می گردد. هوا و مواد فرار تولید شده حین عمل آوری پلی استر در داخل پریفورم از طریق دریچه ی هوای قسمت دریچه سرپوش با ایجاد مکش و خلا به دریچه ی هوا خارج می گردد. بعد از آنکه رزین در داخل پریفورم فیبری کاملا عمل آوری شد، درپوش ها در دو انتهای لوله جهت تکمیل فرآیند برداشته می شود.
فرآیند توسعه داده شده نیازمند زمان عملیاتی کمتر و هزینه کمتر با استفاده از تجهیزات کوچکتر و ساده تر نسبت به تکنولوژی های مبتنی بر عدم حفاری متداول می باشد.
از آنجایی که RTM توانایی ساخت محصولات بزرگ و پیچیده را با قیمت پایین دارد، کاربرد فرآیند RTM برای تعمیر و مقاوم سازی خطوط لوله ی زیر زمینی بسیار بزرگ قابل پذیرفتن است.
هر چند این روش برای مقاوم سازی لوله های بتنی آب و فاضلاب پیشنهاد و توسعه داده شده است ولی میتوان از آن در پارهای موارد خاص، برای خطوط لوله کم فشار فولادی نیز استفاده کرد.
استفاده از محصولات پیش عمل آوری شده در تقویت لوله های بتنی با پوشش های کامپوزیتی (Precured Composite Layers Method)
یکی دیگر از متدهای اصلی تعمیر بر پایه مواد کامپوزیت سیستم پوشش پیش عمل آوری شده است. این سیستم ها از اشکال متنوعی از کامپوزیت ها ، همچون پوشش های پوسته ای، نواری، یا شبکه ای، تشکیل شده که در محل کارخانه ساخته می شوند. در این روش معمولا یک چسب به همراه آستر و بتونه به منظور اتصال مقاطع به سطح بتن بکار می رود. همچنین لازمست توصیه های سازنده سیستم در مورد نحوه اتصال بررسی شود. عملکرد سیستم های پیش عمل آوری شده مشابه بتن های پیش ساخته می باشد . سه نوع متداول سیستم های پیش عمل آوری شده عبارتند از:
- صفحات با ساختار لایه ای تک جهته پیش عمل آوری شده که معمولا به صورت بندیل های تخت یا طاقه هایی از نوارهای نازک به کارگاه ارسال می گردند.
- شبکه با راستای چند جهته الیاف که به صورت رول شده به محل ارسال می شوند.
- پوسته های پیش عمل آوری شده که معمولا به صورت اجز ای پوسته ای با برش طولی به محل فرستاده می شوند به نحوی که پس از باز نمودن بسته بندی ها و قرار گرفتن اجزاء کنار یکدیگر در اطراف لوله ، لایه های پوسته ای به لوله می چسبند و نقش محصور نمودن بتن در مقابل بارهای لرزه ای را ایفا می کنند.
سیستم پوشش پیش عمل آوری شده بر خلاف سیستم چسباندن تر که دارای مزیت انعطاف پذیری بوده و می توان آن را برای لوله ها با هندسه و قطر متغیر بکار برد، را تنها می توان برای یک قطر لوله معین با هندسه مشخص ساخت. در مقابل و بدلیل داشتن نسبت فیبر به رزین بیشتر، این محصولات در مقایسه با همتایان خود که به روش درجا تولید میگردند، مقاومت و سختی بیشتری را نشان میدهند.
کامپوزیت پلیمری FRP سوپر لمینت مقاوم سازی افزیر (FRP Super Laminate Method)
بر طبق برگه ی گزارش ASCE منتشر شده در سال 2009 برای زیر ساخت های آمریکا، لوله های دارای نشتی روزانه در حدود 7 بیلیون گالن آب شرب پاک (26 بیلیون لیتر) از دست می دهند. بعلاوه، تعداد زیادی از خطوط لوله در شبکه ی توزیع آب و همچنین در صنایع نفت، مواد شیمیایی و نیرو بصورت جدی آسیب دیده و نیازمند تعمیر یا مقاوم سازی می باشند. این لوله ها عموما تحت فشار می باشند و هرگونه آسیب المان مقاوم سازی شده در لوله های استوانه ای بتنی پیش تنیده و یا کاهش ضخامت در لوله های فولادی مقاومت لوله در مقابل تنش های حلقوی داخلی را کاهش می دهد. در صورت عدم مراقبت، پیامدهای چنین گسیختگی هایی بسیار خطرناک بوده و می تواند باعث به زیر آب رفتن کل منطقه و یا تعطیل شدن اجباری و فوری یک نیروگاه گردد.
به مدت دو دهه جامعه مهندسین از پارچه های کامپوزیتی به صورت روش چسبیدن تر یا ورقه ها به منظور مقاوم سازی لوله های بتنی آب و فاضلاب استفاده می نمود. الیاف یک مجرای فشاری با مقاومت کافی در جهت های محیطی و طولی در داخل خط لوله ایجاد می کنند. اگرچه این روش بسیار موثر بوده، فی الذات دارای نقایصی هستند، از جمله زمان بالای مورد نیاز جهت ساخت بر مبنای متد چسباندن تر، خصوصا هنگامی که طول خط لوله نیازمند چنین نوع تعمیر زیاد باشد، که سبب میشوند مهندسین قادر به ارائه راهکارهای باکیفیت و در عین حال کم هزینه برای تعمیر آسیب و خوردگی لوله های بتنی آب و فاضلاب نباشند.
کامپوزیت های پلیمری سوپر لمینت نسل جدیدی از محصولات بر پایه FRP ارائه شده توسط مقاوم سازی افزیر هستند با انعطاف بالا که به تازگی برای غلبه بر انواع آسیب و خوردگی لوله های بتنی آب و فاضلاب ذکرشده، توسعه داده¬شده¬اند. این پوشش ها در مقابل فیبرها و دیگر نوارهای پوششی نازک تر که تا به امروزه در دسترس بوده دارای مزایای عمده ای بوده، بسیاری از کاربری هایی که برای دهه ها مهنسین و کارشناس های عرصه ساخت و ساز به چالش می کشید را امکان پذیر کرده است.
فرآیند نصب شامل به کاربردن یک لایه نازک اپوکسی به عنوان بتونه جهت نگهداری سوپرلمینت و اتصال آن به سطح لوله می باشد. از آنجایی که سوپرلمینت پیش عمل آوری شده اند و هیچ گونه حباب هوایی وجود ندارد، نیازی به برطرف کردن حباب هوا نمی باشد. بر حسب قطر لوله، به علت حافظه الاستیک، سوپرلمینت دورپیچ شده به راحتی داخل لوله باز شده و به لوله میزبان می چسبد.
اگر قطر لوله کوچک باشد و امکان ورود انسان به داخل آن وجود نداشته باشد، خط لوله را می توان با استفاده از یک پکر (Packer) تعمیر کرد. پکر ها قالب های به شکل استوانه هستند که یک کیسه ی بسته بر روی سطح خارجی آن وجود دارد. یک طول مناسب از سوپرلمینت را میتوان برید و سطح آن را با بتونه اپوکسی پوشاند؛ سپس لمینت به دور پکر پیچیده شده و با استفاده از ریسمان در جایش ثابت می شود. سیستم مونتاژ شده از طریق دریچه های دسترسی به داخل لوله وارده شده و با استفاده از دوربین های مدار بسته به مکان مورد نظر کشیده می شود. در ادامه، پکر متورم شده و اجازه می دهد تا سوپرلمینت به لوله میزبان بچسبد. بعد از چند دقیقه هوای داخل پکر جمع شده و از لوله خارج می گردد. قطعات اضافی می تواند به همین شیوه با یک طول همپوشانی کوچک جهت تعمیر یا مقاوم سازی طول بیشتری از لوله نصب گردد.
هزینه تعمیر و تقویت و مقاوم سازی لوله بتنی به کمک مصالح کامپوزیت پلیمری FRP
صفحات خارجی فولادی متصل شده، پوشش های فولادی یا بتنی مسلح شده و مقاوم سازی خارجی با استفاده از سیم و آهن تکنیک های سنتی مورد استفاده جهت تامین مقاومت بیشتر، برطرف کردن نواقص طراحی، اصلاح مشکلات ناشی از فرسودگی یا بهبود عملکرد مورد نیاز با تغییر آیین نامه ها، در سازه های بتنی موجود به منظور مقاوم سازی و تقویت آن ها بوده است. بعلت نیاز به تجهیزات سنگین هزینه به کار گیری این تکنیک ها بالا بوده و در بیشتر موارد عمر سرویس دهی بلند مدتی را فراهم نمی کنند. از آنجایی که مواد کامپوزیتی بسیار سبک می باشند، فرآیند نصب کامپوزیت ها بر روی یک سازه و در این مبحث خطوط لوله بسیار آسان شده و در بیشتر موارد، تجهیزات سنگین جهت تعمیر مورد نیاز نمی باشد. هچنین، از آنجا که چگالی مصالح FRP چهار تا شش بار کمتر از چگالی فولاد می باشد. در نتیجه ی کاهش چگالی، آسانی جابجایی و کاهش هزینه حمل و نقل و بالطبع کاهش هزینه تمام شده ی مقاوم سازی را شاهد خواهیم بود.
اگرچه الیاف و رزین های مورد استفاده در سیستم های FRP نسبت به دیگر مصالح متعارف مانند بتن و فولاد گرانتر هستند، ولی به علت سهولت ساخت و صرفه جویی در زمان، کاهش هزینه های مربوط به دستمزد و تجهیزات نصب سیستم های FRP، هزینه ی نهایی تعمیر قابل رقابت با دیگر روش ها می باشد.
برای دریافت اطلاعات جامع درباره قیمت و هزینه انواع روش¬های مقاوم سازی لوله های بتنی آب و فاضلاب با استفاده از کامپوزیت پلیمری FRP مقاوم سازی افزیر کافی است با متخصصین شرکت در تماس باشید.
شرکت مقاوم سازی افزیر که از پیشگامان و پیشروان حوزه مقاوم سازی لوله بتنی آب و فاضلاب میباشد، آماده ارائه خدمات موردنیاز شما در سراسر کشور می باشد. برای دریافت اطلاعات بیشتر، مشاوران ما در هر لحظه آماده پاسخگویی به شما می باشند.
سلام
چه روش هایی برای مقاوم سازی لوله های بتنی آب و فاضلاب وجود دارد ؟
با سلام و احترام
با روش های مختلفی همچون استفاده از کامپوزیت FRP ، استفاده از کامپوزیت FRCM و استفاده از غلاف کامپوزیت ، استفاده از ژاکت بتنی و روش های ترکیبی میتوان لوله های بتنی را مقاوم سازی نمود