مقاوم سازی لوله فولادی با FRP
یکی از راهکارهای نوین تقویت و بهسازی خطوط لوله فولادی استفاده از کامپوزیت های پلیمری تقویت شده با الیاف FRP می باشد. با گذشت زمان، خطوط لوله فولادی همواره در معرض آسیب دیدگی هایی همچون خوردگی قرار می گیرند. محصولات تولید شده از فیبرهای مسلح شده با الیاف اف آر پی (FRP)، که دارای ویژگی هایی همچون مقاومت مناسب در برابر خوردگی، سادگی اجرا در محل نصب و سبکی می باشند، با کاهش تنش های بوجود آمده در جداره لوله، نقش کلیدی در کاهش آسیب های وارد به آن به عنوان یکی از شریان های حیاتی خواهد داشت.
خطوط لوله فولادی، جهت انتقال نفت و گاز و همچنین آب و فاضلاب به طور گسترده ای استفاده قرار گرفته است. هرگونه خسارتی که به یکی از بخش های ضعیف این شبکه وارد آید بر تمامی مجموعه اثر گذاشته و باعث ناکارآمدی کل سیستم می گردد. در واقع سامانه های خطوط لوله فولادی به عنوان یکی از شریان های حیاتی در کاهش و یا افزایش خسارات و آسیب پذیری ناشی از خطرات پدیده هایی همچون زمین لرزه نقش کلیدی دارند، چرا که شکست لوله های گاز و نفت سبب بروز آتش سوزی می گردد، تخریب شبکه ی فاضلاب سلامت بازماندگان را به مخاطره می اندازد و قطع شبکه ی آبرسانی نیز بازماندگان را در مضیقه قرار می دهد. بنابراین، لزوم شناخت انواع راهکار های تقویت و بهسازی خطوط لوله فولادی همچون هر سازه ی دیگر در معرض آسیب، امری اجتناب ناپذیر می باشد. در بسیاری از موارد، جایگزین کردن لوله آسیب دیده با یک لوله جدید بدلیل هزینه بالا و زمان بر بودن عملیات تعویض امکان پذیر نمی باشد. به همین منظور محصولات تولید شده از فیبرهای مسلح شده با الیاف (FRP)، خصوصا کامپوزیت های پلیمری تقویت شده با الیاف کربن (CFRP)، که اغلب با نیاز کم به حفاری و یا حتی بدون نیاز به حفر ترانشه نصب گردیده به عنوان راه حلی مناسب جهت مقاوم سازی خطوط لوله فولادی پیشنهاد می گردد. سیستم FRP بدین صورت تعریف می شود که الیاف و رزین ها برای ساخت چند لایه مرکب مورد استفاده قرار می گیرند، به نحوی که رزین های مصرفی به منظور چسباندن چندلایه مرکب به سطح مورد نظر و پوشش ها به منظور محافظت مصالح ترکیب شده استفاده می شوند. این مصالح به شکل های مختلف و درگستره ای از انواع ورقه های چند لایه کارخانه ای گرفته تا ورقه های خشک قابل پیچش روی اشکال مختلف سازه ای قبل از اضافه کردن رزین قابل دسترس می باشند.
در گذشته ای نه چندان دور مدارک فنی بسیارمحدودی در این رابطه وجود داشت، لیکن امروزه تعداد قابل توجهی از مقالات علمی، نشریات و کنفرانس های مربوط به بحث کاربرد این مصالح در مقاوم سازی اختصاص دارد . این رشد فزاینده شاهد رویکرد و اهمیت این فناوری نو می باشد که به دنبال گسترش نیاز و توجه به تقویت با استفاده از مصالح کامپوزیت و به منظور کاربردی نمودن دانش فنی، روش های طراحی نیز تدوین گردیده اند تا دربخش حرفه مورد استفاده قرار گیرند. تبیین روش های تحلیل و در نظر گرفتن ضرایب ایمنی در طراحی با ملاحظات اقتصادی منجر به تدوین دستورالعملها و آیین نامه های محاسباتی و اجرایی در این حوزه شده است.
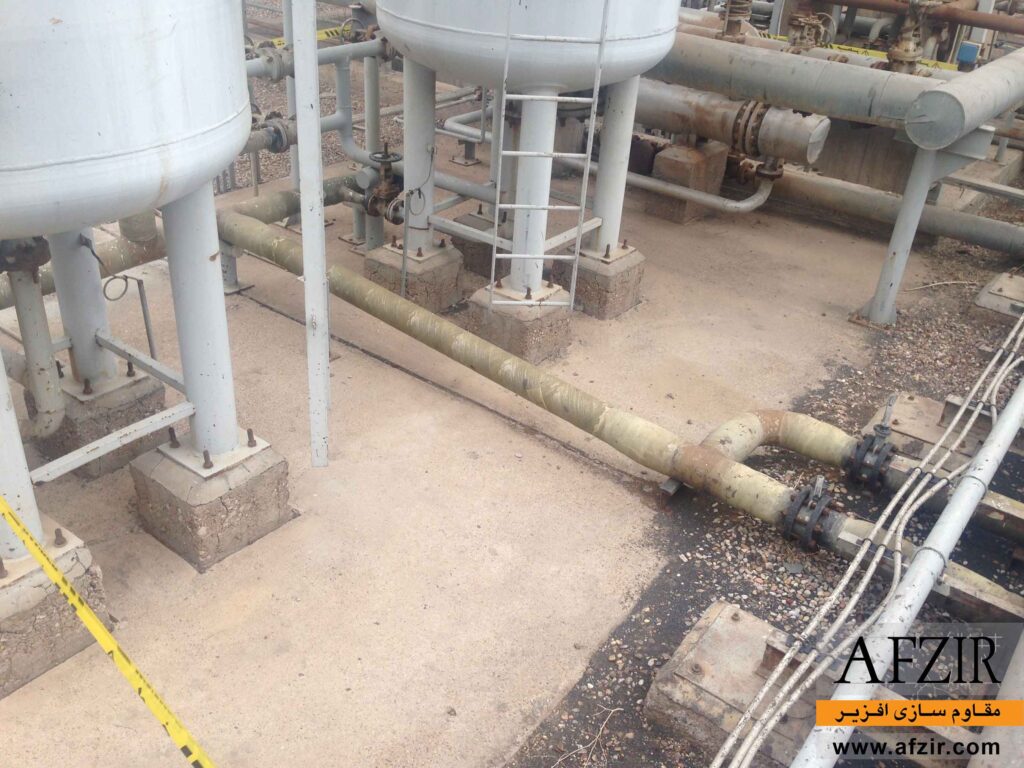
آسیب های وارد بر لوله های فولادی در صنعت
آسیب های وارد بر لوله های فولادی در صنعت نفت و گاز
در جوامع مدرن، سامانه هاي گازرساني، انرژي مورد نياز براي حمل و نقل و توليد برق را تأمين كرده و در توليد كالاهاي مورد نياز و ارائه سرويس های ضروری از قبيل تامين گرماي مورد نياز و ساير موارد نيازمند انرژی برای حفظ زندگی در سطح مطلوب، مورد استفاده قرار ميگيرند.
فولاد را می توان پرکاربرد ترین مصالح برای ساخت لوله ها در صنایع نفت و گاز دانست. باوجود بیش از 1/7 میلیون کیلومتر از خطوط لوله گاز، نفت خام و محصولات پتروشیمی در سرتاسر دنیا، جابجایی نفت و گاز با استفاده از خطوط لوله فولادی آشکارا نقش کلیدی در تامین نیاز روزافزون انرژی بازی می کند.
تعداد بیشماری از این خطوط لوله از دهه های 1940 و 1950 در دست کاربری هستند. آسیب های وارده به خطوط لوله می تواند ناشی از فرسودگی خط لوله در گذر زمان، ضربات تصادفی وارده به آن ها، دامنه گسترده تغییرات دمایی 130- تا 50 درجه سانتیگراد، فشار بالا، خوردگی شیمیایی و یا شرایط سخت محیطی باشد که هر کدام از آن ها می تواند یکپارچگی خط لوله را تحت تاثیر سوء قرار دهد. به طور خلاصه از جمله انواع آسیب و خرابی لوله های فولادی نفت و گاز می توان به موارد زیر اشاره کرد:
- خرابی مکانیکی
- کمانش
- فرورفتگی در اثر ضربه
- خستگی
- اتصالات ضعیف
- خرابی شیمیایی
- خوردگی لوله های فولادی نفت و گاز در سطح داخلی (در اثر CO2، H2S، باکتری ها، آب شور)
- خوردگی لوله های فولادی نفت و گاز در سطح خارجی (استفاده از پوشش های نامناسب و …)
- خرابی ناشی از خطا در ساخت و نصب
- ضعف جوشکاری (عمق کم جوش، ترک خوردگی جوش، حفره ای شدن جوش و …)
- آسیب لوله های فولادی نفت و گاز در اثر ضربه
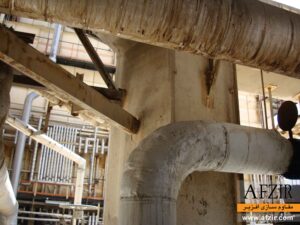
انواع پیامدهای ناشی از آسیب ها و خرابی ها در جدول زیر آورده شده است.
طبقه بندی پایه خرابی های خطوط لوله نفت و گاز | |||
آسیب های فیزیکی وارده به دیواره لوله | تنش بیش از اندازه یا آسیب های ناشی از خستگی | آسیب و یا پارگی پوشش خارجی | آسیب و یا گسیختگی قسمت های مختلف |
خوردگی (داخلی و خارجی) | خم شدن بیش از حد بدون کمانش | آسیب های وارده بر پوشش غیر از عامل خوردگی | آسیب های وارده بر دریچه، گسیختگی یا نشت |
خراش پوشش شیار افتادن فرورفتگی |
آسیب های ناشی از خستگی | آسیب های وارده بر پوشش ناشی از بار ثقل | آسیب وارده بر فلنج یانشت فلنج |
سوراخ شدن | بار فشاری وارده بیش از حد | آسیب های قطبی، اتلاف یا تخلیه | آسیب وارده به اتصالات یا نشت آن ها |
گسیختگی | |||
ترک برداشتن |
آسیب های وارد بر لوله های فولادی در صنعت آب و فاضلاب
لوله های فلزی نیز در صنعت آب و فاضلاب کاربرد بسیاری دارند. لوله های فلزی شامل لوله های گالوانیزه و نیز لوله های چدنی از انواع اصلی لوله هایی هستند که به منظور جمع آوری و انتقال آب و فاضلاب مورد استفاده قرار می گیرند.
لوله های گالوانیزه خود به دو دسته تقسیم می شوند: لوله های فولادی گالوانیزه و لوله های آهنی گالوانیزه. این دو نوع در بازار به لوله های آهنی سفید معروف اند و تنها تفاوت آنها در براق و سبکتر بودن نوع فولادی آن می باشد. هر دو نوع لوله های گالوانیزه در شاخه های 6 متری ساخته می شوند و در هر دو سر حدیده شدهاند. قطر اسمی این لوله ها تا 232 سانتی متر دسته بندی شده اند. لوله های فولادی گالوانیزه برای آبرسانی و گاهی برای تخلیه فاضلاب به کار برده می شوند ولی مورد استفاده اصلی آنها برای تهویه است. جنس این لوله ها از فولاد نرمی است که در ساختن آن ورقه فولاد را با فشار داخل قالب عبور داده و درز آن را جوش می دهند و سپس آنها را جهت افزایش مقاومت در برابر اسیدها و زنگ زدگی ها روی اندود ( گالوانیزه ) می کنند. این نوع لوله ها نسبت به نوع آهنی در برابر اسیدها مقاومت کمتری دارند. جنس لوله های آهن گالوانیزه از آهن سفید نورد شده است که درز آن توسط دستگاه های درز جوش بهم جوش داده می شود و سپس لوله را در فلز روی مذاب فرو می برند. این لوله ها از رنگ تیره و خاکستری شان شناخته می شوند. برای اتصال لولههای گالوانیزه نمیتوان از فرایند جوشکاری استفاده نمود. چرا که در اثر حرارت جوشکاری روی موجود در این لولهها اکسید شده و گاز اکسید روی ایجاد شده برای تنفس خطرناک است.
جنس لوله های چدنی نیز از چدن ریخته گری است و بر حسب نوع کاربرد، مقدار آلیاژ، شکل و طول لوله و نوع اتصالات با هم متفاوت است و اغلب در سیستم لوله کشی فاضلاب و برای جمع آوری آب های سطحی استفاده می شوند. این نسل لولهها که استفاده از آنها تا حدود زیادی منسوخ شده است جزء نسلهای اولیه لوله کشی فاضلاب به شمار میآمدند.
مزایای لوله های چدنی عبارتند از:
- مقاومت و استحکام در برابر فشار خارجی
- فرسودگی کمتر از لولههای فلزی
- قابلیت استفاده از دستگاه تراکم هوا جهت باز نمودن سیستم
- پایینتر بودن قیمت نسبت به لولههای آهنی
- بالا بودن استانداردهای بهداشتی جهت فاضلابهای عفونی و سمی
سنگینی وزن و اجرای بسیار دشوار و همچنین زنگ زدن تحت تاثیر مواد شیمیایی از جمله معایب این جنس خطوط لوله می باشد.
خوردگی یکی از مهمترین و هزینه برترین عوامل آسیب و خوردگی لوله های فولادی آب و فاضلاب است.
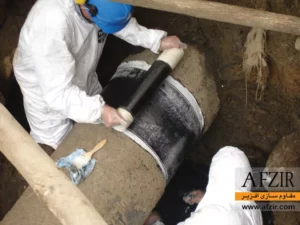
آسیب و خوردگی لوله های فلزی آب و فاضلاب بر اساس دسته بندي مودهاي آسيب و خرابي در زلزله هاي گذشته عبارتند از:
- شكل خسارات به تفكيك نوع لوله متفاوت است.
- در لوله هاي چدني شكل پذير اتصال عادي لوله اغلب جدا شده و نشت آب و یا فاضلاب به وجود آمده است.
- در لوله هاي چدني و لوله هاي PVC سخت، جدايي و شكستگي قطعه اتصال و شكستگي در بدنه لوله ديده ميشود.
- در لوله هاي فولادي خطوط لوله آب در قطعه اتصال جوش داده شده و بدنه لوله شكستگي وجود داشته است. همچنين همراه با شكستگي در تكيه گاه پل لوله شكستگي در بدنه لوله نيز در چند محل مشاهده شده است.
- در زمينه قطعات وابسته خطوط لوله آب، خسارات شير آتشنشاني و دريچه ها شكستگي و شل شدن بخش لبه و همچنين شكستگي در بدنه مشاهده شده است.
با توجه به موارد فوق مودهاي آسيب اصلي در لوله ها عبارتند از:
- شكستگي
- ترك محيطي حلقوي
- ترك طولي (در لوله های آب) و ترک عرضی (در لوله های فاضلاب)
- شكستگي بدنه لوله
- شکاف در اتصال
انواع روش های مقاوم سازی خطوط لوله فولادی با استفاده از FRP
همانگونه که در مقدمه اشاره شد، خطوط لوله فولادی با گذشت زمان همواره در معرض مسائلی همچون خوردگی، کمانش، خستگی، شکست و … می باشند، به همین علت هرگونه آسیب به اين سامانه ها منجر به قطع جريان گاز و اخلال در سیستم خطوط لوله آب و فاضلاب شده و منجر به حوادث ثانويه مانند انفجار، آتش سوزي و مسموميت می شود.
در صورت عدم آگاهي از ميزان آسيب پذيري براي تأمين مقاومت و ايمني لازم و عدم انجام بهسازی كافي، عواقب و خسارات ناشي از آسیب دیدگی افزایش يافته و با عدم توانايي مهار مناسب، شرايط اضطراري مي تواند منجر به رويداد فاجعه و بروز شرايط بحراني گردد.
اهمیت انتخاب روش صحیح، دقیق و متناسب مقاوم سازی خطوط لوله فولادی در رعایت نکات فنی و مهندسی، مدیریت بهینه ریسک و مدیریت هزینه و کاهش بار مالی پروژه است. به عبارت بهتر، یک متخصص مقاوم سازی خطوط لوله باید بتواند راهکارهایی را برای جلوگیری از انواع آسیب و خوردگی لوله های فولادی ارائه و پیشنهاد کند که در عین کارایی و کارآمدی، جنبه های اقتصادی طرح مورد نظر مقاوم سازی را نیز لحاظ کرده باشد.
در روش های سنتی مقاوم سازی خطوط لوله فولادی، قسمت آسیب دیده از مدار خارج شده، با جوش دادن ورق تقویت شده و دوباره نصب میشود و یا اینکه درصورت نیاز به طور کامل تعویض می گردد. اینگونه روش های مقاوم سازی لوله فولادی، مشکلات متعددی از جمله لزوم قطع شبکه گاز یا آبرسانی و یا دفع فاضلاب را به دنبال دارد. همچنین در بسیاری از موارد، جایگرینی لوله آسیب دیده با یک لوله جدید بدلیل هزینه بالا و زمانبری عملیات تعویض امکان پذیر نمی باشد. با توجه به وجود این مشکلات در روشهای سنتی مقاوم سازی لوله های فولادی، از حدود 20 سال قبل، روش جدیدی تحت عنوان روش مقاوم سازی لوله فولادی به کمک کامپوزیت های پلیمری FRP مورد توجه قرار گرفته است. در این روش از لایه های کامپوزیت با الیاف شیشه (GFRP)، کربن (CFRP) و یا آرامید (AFRP) استفاده می شود.
از مزایای این مواد می توان به مقاومت کششی و سختی بالا، وزن کم، مقاومت در برابر خوردگی، نصب آسان در فضاهای محدود، کاهش در هزینه های نیروی انسانی، قابلیت نصب در طول های زیاد و قابلیت نامحدود در اندازه و ابعاد و هندسه اشاره نمود.
پیشنهاد متخصصین مقاوم سازی افزیر استفاده از محصولات کامپوزیت پلیمری FRP این شرکت است. متخصصین مقاوم سازی لوله فولادی شرکت افزیر با تلفیق دانش و تجربه فراوان در زمینه تعمیر، تقویت و مقاوم سازی خطوط لوله فولادی، به کمک مصالح کامپوزیت پلیمری FRP برای انواع آسیب و خوردگی های ذکرشده، زاویه های الیاف و تعداد لایه های مورد نیاز با توجه به فشار وارده متناسب با استانداردهای طراحی و مقدار و وسعت خوردگی و آسیب در لوله را محاسبه کرده و با توجه به شرایط شیمیایی و حرارتی محل رزین مناسب را برگزیده، راهکار و محصول متناسب با نیاز شما را ارائه می کنند. لایه های کامپوزیت پلیمری FRP مقاوم سازی افزیر به صورت پارچه هایی تهیه شده، به رزین آغشته شده و به وسیله کارگران متخصص با زاویه های استاندارد، به روش پیچش روی لوله هایی که سطح آن از پیش آماده شده پیچیده می شود.
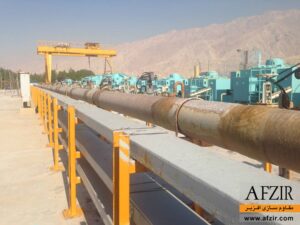
از جمله مزایای فراوان روش مقاوم سازی لوله فولادی به کمک مصالح کامپوزیت پلیمری FRP مقاوم سازی افزیر، می توان به موارد زیر اشاره کرد:
- در روش مقاوم سازی لوله های فولادی به کمک مصالح کامپوزیت پلیمری FRP مقاوم سازی افزیر، هزینه های مربوط به جوشکاری و قطع سیستم گاز یا آب و فاضلاب در لوله حذف می شود.
- این روش قابلیت بازگرداندن لوله های آسیب دیده در اثر انواع آسیب و خوردگی لوله های فولادی به وضعیت اولیه طراحی را دارا است و همچنین از خوردگی آن ها در آینده جلوگیری می کند.
- خطوط لوله به هنگام تعمیر می توانند در شرایط و فشار کاری معمولی خود، کار کنند و نیازی به قطع شبکه نیست. هم چنین در این روش گاز یا آب به هدر نخواهد رفت.
- به علت وزن کم مواد کامپوزیت، نصب آن بسیار راحت است و تعمیر به وسیله دو نفر بدون نیاز به لوازم و دستگاه های خاصی انجام می شود.
- با توجه به عدم نیاز به قطع شبکه گاز، آب یا فاضلاب، تکه تکه کردن لوله و جوشکاری به هنگام تعمیر، در زمان هم صرفه جویی خواهد شد.
در ادامه انواع راهکارهای به کار رفته جهت مقاوم سازی خطوط لوله فولادی به کمک مصالح کامپوزیت FRP مقاوم سازی افزیر به صورت کامل شرح داده می شود.
روش چسباندن تر در تقویت لوله های فولادی با بوشش های کامپوزیتی (Wet Lay-up Method)
بیشتر لوله های فولادی مورد استفاده را می توان ذیل عنوان لوله های با فشار متوسط تا فشار بالا دسته بندی کرد. خوردگی فولاد منجر به کاهش ضخامت دیواره و در ادامه کاهش مقدار مقاومت و مقدار فشار می گردد. FRP می تواند به منظور ایجاد یک مجرای فشار در داخل لوله جهت مقاومت در برابر تمام یا بخشی از فشار مورد استفاده قرار گیرد.
روش چسباندن تر پایه ترین متد تعمیر خطوط لوله می باشد. به مانند تمامی تکنیک های مورد استفاده جهت تعمیر، سطح خطوط لوله باید تمیز و آماده سازی گردد. بیشتر طراحی ها بر این فرض استوار است که بعد از اتمام تعمیر تنش ها در سطح لوله تواما توسط لوله فولادی و پوشش FRP تحمل می شود. این فرض مستلزم اتصال مناسب بین FRP و لوله میزبان می باشد. پاشیدن ماسه با فشار بالا تا رسیدن به سطح سفید رنگ فلز یکی از آماده سازی های مرسوم سطوح این گونه لوله ها می باشد. سطح خط لوله باید با استفاده از فشار هوا تمیز شده به طوری که هرگونه مصالح سست از روی آن برداشته شود. در صورتی که سیستم رزین مورد استفاده نسبت به رطوبت حساس می باشد، اقدامات مورد نیاز جهت جلوگیری از تشکیل رطوبت بر روی سطح لوله باید در نظر گرفته شود. در بیشتر موارد جریان پر فشار هوا به منظور ایجاد تهویه برای افراد به هنگام کار در داخل خط لوله برقرار می گردد. دمای هوا را می توان به منظور حصول اطمینان از خشک بودن سطح لوله به هنگام تعمیر تنظیم کرد.
تمامی قسمت هایی که دارای شرایط بسیار نامناسب یا حفره های کوچک می باشند را می توان قبل از به کار بردن FRP تعمیر و یا وصله کرد. حفره های کوچک تر (در حدود 30 میلیمتر) را می توان با لایه های بیشتر FRP تعمیر کرد. برای حفره های بزرگتر، ممکن است جوش دادن یک ورق فلزی بر روی قسمت آسیب دیده مورد نیاز باشد. برخی از خطوط لوله ممکن است به علت استفاده از پرچ یا درز جوش دارای پیش آمدگی باشند. اقدامات مورد نیاز به منظور صاف کردن این سطوح باید صورت گیرد. معمول ترین اقدام در این موارد اعمال یک پوشش از اپوکسی با خاصیت ویسکوزیته بالا بر روی آن سطوح می باشد. رزینی که برای اشباع کردن فیبرها استفاده شده است را می توان با استفاده از فوم سیلیکا ( برای مثال کابوسیل) در این نواحی برای این کاربرد ضخیم کرد. کربن و فولاد عناصر ناهمسان می باشند و به هنگام تماس با یکدیگر خوردگی گالوانیگ می تواند در پی داشته باشند. بهتربن راه برای جلوگیری از این نوع خوردگی تعبیه یک عایق دی الکتریک بین فیبرهای کربن (CFRP) و خط لوله فولادی می باشد. اگرچه رزین اپوکسی موجود در FRP تمامی فیبرها را کاملا می پوشاند، ضخامت نازک رزین عمدتا به عنوان یک حایل محافظ مناسب برای جلوگیری از تماس در دراز مدت در نظر گرفته نمی شود. عمده راهکار مقبول در صنعت بکارگیری لایه ای از الیاف شیشه (GFRP) به عنوان لایه ی اول برای بیشتر تعمیرات انجام گرفته در خطوط لوله فولادی می باشد.
اگر فیبر شیشه (GFRP) به عنوان افزایش دهنده ی مقاومت خط لوله در نظر گرفته نشود، یک لایه نازک از الیاف به وزن تقریبی 300 گرم بر متر مکعب یا کمتر برای چنین منظوری می تواند مورد استفاده قرار گیرد.
فرآیند اشباع کردن فیبر می تواند توسط ماشین های اشباع ساز که از دو غلطک برای انتقال با فشار رزین داخل فیبر خشک استفاده می کند صورت گیرد. فاصله ی بین دو غلطک باید به منظور حصول اطمینان از نسبت صحیح رزین به فیبر، فیبر اشباع شده به طور صحیح تنظیم شود. بیشتر محصولات تقریبا نسبت حجمی برابری از رزین به فیبر را نیاز دارند. فیبر اشباع شده که به طور خودکار در اطراف تیوپ PVC می چسبد، به کارگران جهت نصب بر روی سطح خط لوله تحویل داده می شود. بر حسب قطر خط لوله، طول تعمیر و مجاورت آن به ورودی های دسترسی، فرآیند اشباع سازی می تواند داخل و یا خارج خط لوله انجام گیرد. برخی از پیمانکاران دارای تجهیزات اشباع سازی با قابلیت جداسازی می باشند که می توان آن ها را جهت عبور از یک ورودی دسترسی 60/96 سانتی متر از یکدیگر جدا کرد. تجهیزات در داخل خط لوله می تواندد به سرعت بر روی یکدیگر سوار بشوند.
از آنجا که مقاومت محصولات FRP به راستا و مقدار فیبر در هر جهت بستگی دارد دارای خواص غیر ایزوتروپیک می باشند. از آنجا که بیشتر تنش های ایجاد شده در خط لوله ناشی از فشار داخلی در جهت دورانی می باشند غیر ایزوتروپیک بودن FRP ها یک مزیت فوق العاده جهت تعمیر خطوط لوله می باشد. بنابراین بخش عمده ای از فیبرها در جهت دورانی چرخانده می شوند. انحنا و تغییر جهت منجر به ایجاد سوراخ در طول لوله می شود. در صورت نیاز، تنش های ایجاد شده را می توان با فیبر های تعبین شده به موازات محور خط لوله مهار کرد.
به عنوان بخشی از پروسه طراحی، تعداد لایه ها و راستای الیاف تعیین می گردد. فیبر های کربن (CFRP) را می توان به صورت یک سویه و یا دو سویه و به شکل لوله هایی با عرض 300 تا 1300 میلیمتر و طول 60 تا 90 متر ساخت. در فیبرهای یک سویه حجم عمده ای از فیبر در یک جهت ،معمولا در طول فیبر، قرار داده میشود. همچنین ممکن است مقدار اندکی از فیبرها در جهت عرضی جهت نگه داشتن فیبرهای طولی وجود داشته باشد ولی عمدتا در طراحی از مقاومت محدود این فیبرها چشم پوشی می شود. در صورت نیاز، یک یا چند لایه از الیاف در جهت طولی به منظور تامین مقاومت در آن جهت قرار داده می شود.
فیبرهای دومحوره را می توان با قرار دادن میزان متفاوت فیبر در جهت های طولی و عرضی تولید کرد. ملاحظات اقتصادی سبب شده است این الیاف به شکل لوله های عریض تر و به ابعاد نزدیک به 1300 میلیمتر ساخته شود. این فیبرها عمدتا بصورت نوارهایی جهت محیطی با طول پوشش کافی در دو جهت محیطی و طولی تعبیه می شوند.
در کاربرد بالا دقت کافی در هنگام فرآیند نصب به منظور حصول اطمینان از تعبیه درست فیبر ها (در جهت محیطی و یا طولی) باید در نظر گرفته شود. نا شاقولی و یا قرار گرفتن فیبرها به صورت سست بر روی سطح، مقاومت و سختی سیستم پوششی را کاهش می دهد.
انعطاف پذیری فیبرها در کاربرد روش تر امکان استفاده از آن را در انحناها و نواحی خمیدگی در خطوط لوله را فراهم کرده است.
به طور خلاصه این روش نصب انواع مصالح کامپوزیت پلیمری FRP مقاوم سازی افزیر، نیاز به نیروهای متخصص است تا ابتدا فیبرهای کربن (CFRP) یا شیشه (GFRP) را به رزین (Resin) هایی مانند اپوکسی (epoxy) آغشته کرده و به سطح بیرونی لوله چسبانده شود. اجرای این تکنیک نیازمند نیروی کار ماهر بوده تا اطمینان حاصل شود که فیبرها به صورت صحیح قرار گرفته و هیچ¬ گونه حباب هوایی در زیر این پوشش ها وجود ندارد تا به خوبی بتوان مقاوم سازی لوله فولادی را انجام داد.
استفاده از محصولات پیش عمل آوری شده در تقویت لوله های فولادی با پوشش های کامپوزیتی (Precured Composite Layers Method)
یکی دیگر از متدهای اصلی تعمیر بر پایه مواد کامپوزیت سیستم پوشش پیش عمل آوری شده می باشد. سیستم های پیش عمل آوری شده عبارتند از پوشش های پوسته ای، نواری، یا شبکه ای که با چسب مورد استفاده قرار می گیرند. در سیستم پوشش پیش عمل آوری شده، پوشش های لمینت پیش ساخته و کنترل کیفی شده که برای لوله ها با قطر مشخص اندازه گیری شده اند مورد استفاده قرار می گیرند. سیستم پوشش پیش عمل آوری شده بر خلاف سیستم چسباندن تر که دارای مزیت انعطاف پذیری بوده و می توان آن را برای لوله ها با هندسه و قطر متغیر بکار برد، را تنها می توان برای یک قطر لوله معین با هندسه مشخص ساخت. در مقابل و بدلیل داشتن نسبت فیبر به رزین بیشتر، این محصولات در مقایسه با همتایان خود که به روش درجا تولید می گردند، مقاومت و سختی بیشتری را نشان می دهند.
برای نصب محصولات پیش عمل آوری شده روی سطوح آماده سازی شده باید محل نصب بطور یکنواخت و کاملا هموار با چسب آغشته شود مگر درمواردی که کاربری تماس بحرانی مدنظر باشد . لایه های از قبل عمل آوری شده که برای پوشش بکار می روند باید دارای سطوح تمیز و عاری از آلودگی و مطابق با توصیه های سازنده آماده شوند . ورقه ها یا پوسته های قوسی پیش عمل آوری شده باید مطابق با توصیه های سازنده به چسب آغشته شوند . قبل از گیرش چسب با استفاده از غلتک باید حباب های بین لایه ها خارج شوند . چسب را باید به مقدار توصیه شده توسط سازنده سیستم استفاده نمود تا از اتصال کامل لایه ها به یکدیگر اطمینان حاصل شود.
گرچه این نوارهای ورقه ای نسبت به روش چسباندن تر نصب آسانتر و مقاومت بیشتری دارند اما به دو دلیل زیر، استفاده و کاربرد آن ها محدود می شود:
- یک جهته بودن آن ها سبب شده است که فقط در موارد معدودی برای تقویت برشی به کار بروند و بیشتر برای تقویت خمشی استفاده شوند.
- سختی زیاد این ورقها سبب شده است که نتوان آن ها را به صورت دایره هایی با قطر کمتر از 750 میلیمتر درآورد.
همچنین روش ها و تجهیزات کنونی این اجازه را به ما نمی دهند تا ورقه ای با ابعاد بزرگتر تولید کنیم که از نظر کاربری متفاوت هستند. بنابراین وجود چنین نقایص و کمبودهایی غیرقابل چشم پوشی مینماید.
کامپوزیت پلیمری FRP سوپر لمینت مقاوم سازی افزیر (FRP Super Laminate Method)
برای بیش از دو دهه سیستم چسباندن تر که در بخش قبل توضیح داده شد تکنیک اصلی برای تعمیر سازه ها و خطوط لوله با استفاده از FRP بوده است. با این وجود، اخیرا نسل جدیدی از ورق های FRP معرفی شده است که دارای مزایای بخصوصی در برخی کاربردها می باشد.
ورق های FRP با استفاده از تجهیزات ویژه ای که طراحی شده اند ساخته می شوند. نوارهای الیاف کربن (CFRP) و شیشه (GFRP) تا پهنای 1/5 متر با استفاده از رزین اشباع شده و با استفاده از یک دستگاه پرس که فشار و دمای یکنواختی وارد می کند به ورق های سوپر لمینت تبدیل می شود.
این پوشش ها در مقابل فیبرها و دیگر نوارهای پوششی نازک تر که تا به امروزه در دسترس بوده دارای مزایای عمده ای به شرح زیر می باشد:
- به علت استفاده از ترکیبی از فیبر ها ی تک محوره به تنهایی یا با فیبر های دو محوره، پوشش ها در هر دو جهت عرضی و طولی دارای مقاومت می باشند که این مزیت مهم امکان کاربردهای جدیدی را برای کامپوزیت پلیمری سوپر لمینت فراهم می کند. دامنه ی مقاومت کششی پوشش های سوپر لمینت بین 415 تا 1070 مگاپاسکال می باشد.
- پوشش ها در مقایسه با نوارهای پوششی متداول بسیار نازک تر بوده با ضخامت بسیار کمی به اندازه 25/0 میلیمتر به راحتی می توانند جهت پوشش لوله ای با قطر 75 میلیمتر استفاده شوند.
- پوشش ها با دستگاه هایی با استاندارد های کنترل کیفی بسیار بالا ساخته می شوند که منجر به بهبود کنترل سطح نهایی می شود.
- تعمیرات در سایت می تواند با سرعت بیشتری تکمیل گردد.
- مقاومت ورق های پوشش را می توان قبل از نصب تست کرد، در مقابل وقتی روش چسباندن تر مورد استفاده قرار می گیرد، نمونه ها به طور روزانه در کارگاه برای آزمش های آتی تهیه شده و هرگونه مصالح معیوب برای چند روز و تا آزمایش نمونه ها مشخص نمی گردد که این عامل باعث می شود اقدامات اصلاحی به سختی صورت گیرد.
- تعداد و الگوی لایه های فیبرها در ورق های پوششی سوپر لمینت می تواند طوری تنظیم شود که محصولی خاص با انواع آرایش تولید شود که در نتیجه تاثیر به سزایی در کاهش زمان و هزینه تعمیر و تقویت لوله های فولادی خواهد داشت.
به عنوان مثال مقاومت مورد نیاز برای یک خط لوله فولادی ممکن است نیازمند یک لایه از فیبر کربن (CFRP) تک محوره در طول خط لوله و دو لایه فیبر کربن (GFRP) در راستای محیطی باشد. در همین زمان و به منظور جلوگیری از خوردگی گالوانیک یک لایه اضافی از فیبر شیشه (GFRP) باید به عنوان عایق دی الکتریک به کار برده شود. با استفاده از پوشش های سوپر لمینت ، این فرآیند با دورپیچ کردن فیبرهای کربن (CFRP) بین دو لایه نازک از آستر شیشه ای انجام می گیرد. بنابراین و در این مثال یک لایه تنها از پوشش FRP می تواند نیازمندی های سازه ای (برای مثال مقاومت) و ملاحظات طراحی پروژه را برآورده سازد. در مقابل، استفاده از الیاف با روش چسباندن تر ممکن است نیازمند نصب چهار لایه از فیبر در محل باشد: یک لایه از فیبر شیشه ای (GFRP) و سه لایه از فیبر کربنی (CFRP) تک محوره.
همچنین به دلیل اینکه زمان برترین قسمت کار (یعنی آغشته کردن فیبرها و حذف حباب های هوا) در کارخانه انجام میشود به جای داخل لوله، ا
در نیروگاه ها که دما بالا میباشد آیا از الیاف FRP میتوان جهت مقاوم سازی استفاده نمود؟
با سلام و احترام
با اعمال پوشش های ضد حریق میتوان FRP را دماهای بالا نیز استفاده کرد.
سلام چه تعداد لایه از FRP برای مقاوم سازی لوله ها استفاده میکنیم؟
با سلام و احترام
با استفاده از نرم افزارهای طراحی ضخامت و تعداد لایه های FRP را بدست میآوریم.
سلام
آیا قبل از نصب FRP به لوله های فلزی عیب جوش های اتصالات باید برطرف شود؟
با سلام و احترام
خیر لزومی به این کار نمیباشد چون الیاف FRP قابلیت پوشاندن ضعف های جوشکاری را دارند.
سلام و خسته نباشید
FRP را در چه سطوحی از لوله های فولادی میتوانیم نصب کنیم؟
با سلام و احترام
هم در سطوح داخلی و هم در سطوح خارجی میتوان از FRP برای مقاوم سازی استفاده نمود.